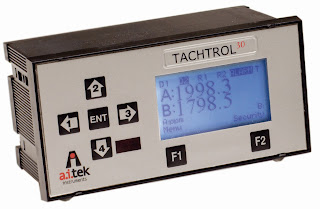
- From the front panel press F2 > Security
- On the drop down menu verify Display Address is not “0”. It can be any number between 1 & 8. If there will be multiple remote displays connected it is best to use 1 for the tachometer.
- If the display address = 0 it must be changed.
- Use the down arrow (4) to navigate to Display Address.
- Press Enter to toggle the address number. Set to the desired number. If there are additional TACHTOL plus units connected, each display must be a different number.
- Press F1 to return to the main screen
Toll Free: 855-288-5330Email: processsales@forberg.com
websites: www.forberg.com & www.autoctrls.com